Fourslide Stamping: What It Is, How It Works, & More on Fourslide Metal Stamping
If you are searching for ways to streamline your business processes, fourslide stamping may be a viable option. Its efficiency and versatility make it ideal for various applications, offering significant cost savings and improved production timelines. Additionally, the technique's capacity for high-volume output without compromising on quality ensures your business can meet demanding production requirements while maintaining exceptional standards.
We’ll explore the ins and outs of fourslide stamping in the coming sections, examining its history, uses, benefits, and more.
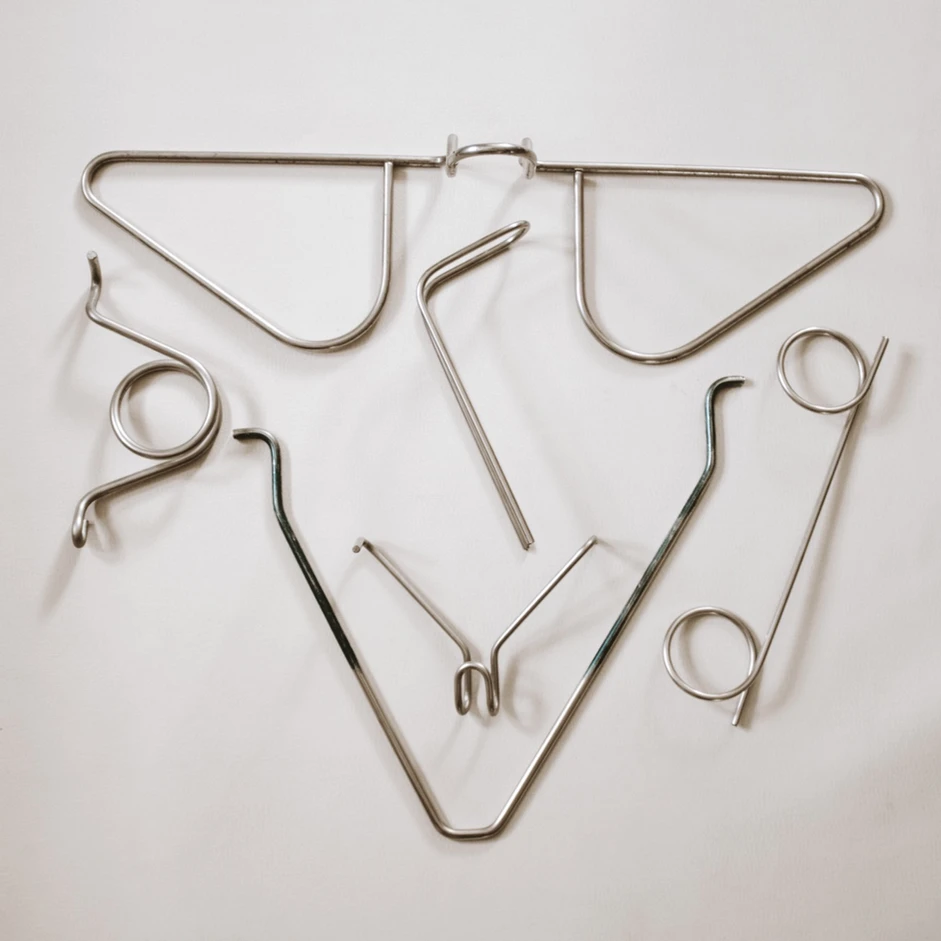
What is fourslide stamping?
Aptly named,
fourslide stampings have four slides, meaning four separate tools attain multiple bends at the same time. In a metal-forming process, a stamping press shapes flat sheet metal is shaped into parts. Through a stamping and forming process, our team produces small and complex components from wire or metal coils.
Unlike traditional power press stamping, which presses together vertically to form the predetermined shape, fourslide metal stamping can move in multiple directions, allowing it to perform numerous operations at one time. Fourslide stamping is the gold standard when manufacturing highly intricate and detailed metal parts in large batches.
Fourslide stamping history
Fourslide stamping has a storied history, dating back to the late 1800s in Connecticut. Seeing exponential growth in a short period of time, by the start of the 1900s, there were three well-known manufacturers of fourslide stamping machines within about 40 miles of one another.
Initially developed in response to the increasing demand for small, intricate metal components, the technique quickly gained traction due to its ability to produce complex parts with extreme precision. The concept was revolutionary at the time, allowing manufacturers to perform multiple operations such as bending, punching, and cutting, all within a single machine cycle.
Rapid evolution
In the decades following its inception, fourslide technology evolved considerably. Innovations in tooling and machine design paved the way for greater versatility and efficiency. During the mid-20th century, the technique saw widespread adoption across various industries, including automotive, aerospace, and electronics, as manufacturers recognized its benefits in producing high-volume, precision parts.
The advent of computerized control systems in the latter part of the century further streamlined fourslide operations, enhancing the capability to produce even more intricate and complex designs.
Fourslide stamping today
Today, fourslide stamping remains a cornerstone of modern manufacturing, renowned for its ability to deliver top-tier, intricate components efficiently and cost-effectively. As technology continues to advance, the scope and applications of fourslide stamping are expected to grow, cementing its status as an indispensable process in the production of detailed metal parts.
How does a fourslide machine work?
A fourslide machine operates through a precisely coordinated system that integrates multiple slides and tools to perform various operations simultaneously. The process begins with a continuous strip or coil of metal being fed into the machine. As the metal advances through the feeding system, it reaches the working area where the slides come into play.
The four primary slides—each positioned at 90 degrees apart—move in sequence, driven by cams and gears configured to ensure exact timing and synchronization. Each slide holds different tools or dies designed to perform specific actions such as bending, punching, cutting, or forming the metal. These slides work in unison to create intricate shapes and complex components in a single cycle.
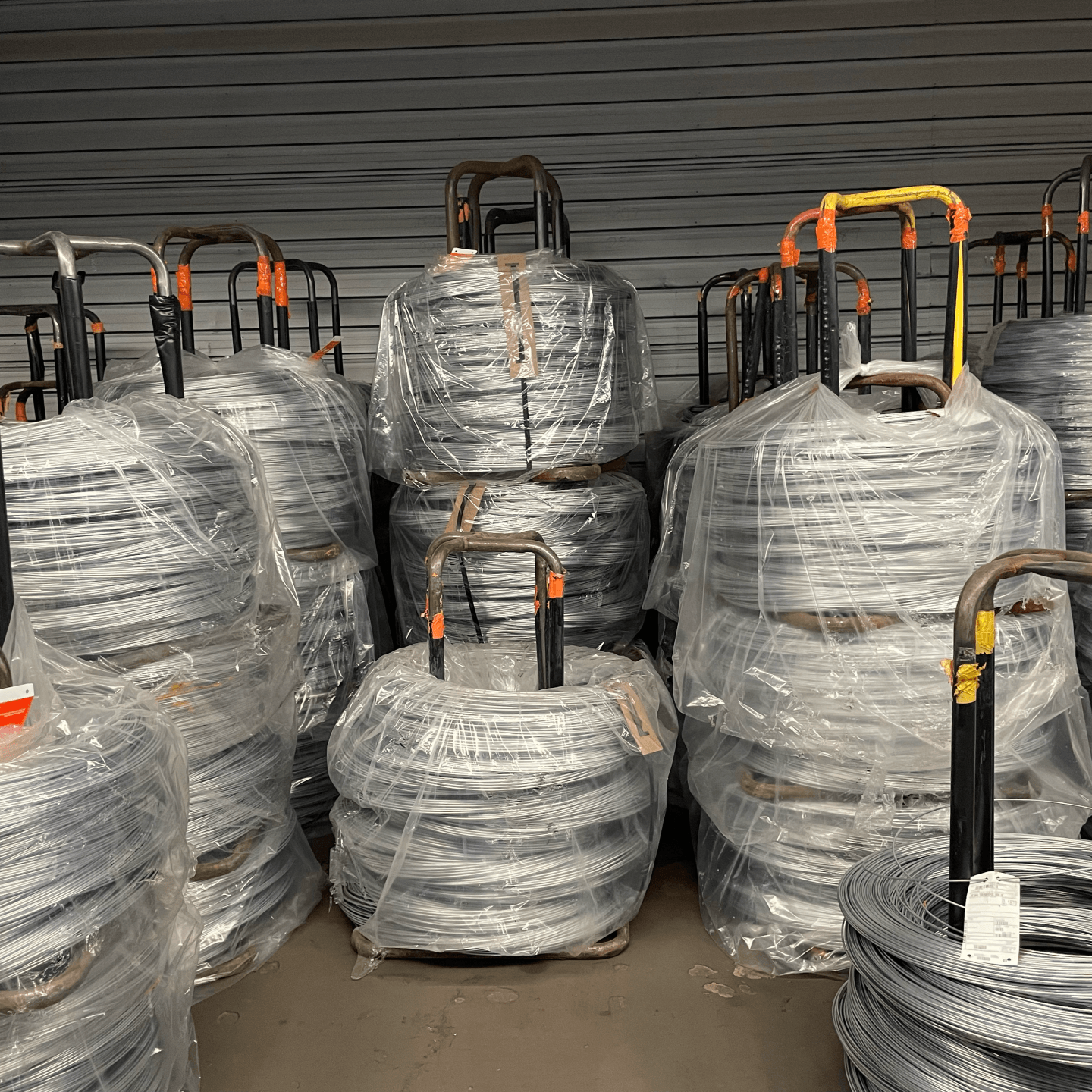
Common materials used in fourslide stamping
Fourslide stamping is compatible with a wide range of materials, enabling manufacturers to meet diverse application needs effectively. Common materials used in this process include:
- Stainless Steel: Known for its excellent corrosion resistance and strength, stainless steel is frequently used in industries such as automotive, medical devices, and consumer electronics. Its robust properties make it ideal for components that require durability and longevity.
- Brass: Brass offers a good balance of strength, workability, and resistance to corrosion.
- Copper: Highly conductive and malleable, copper is an essential material for electrical and electronic components.
- Carbon Steel: Offering various grades based on carbon content, carbon steel provides high tensile strength and is cost-effective. It’s often utilized in automotive parts, industrial machinery, and general hardware applications.
What is fourslide stamping used for?
Fourslide stamping is widely used across multiple industries because of its capacity to make complex, multi-dimensional components with a high level of precision. Its applications are extensive and include the production of intricate parts for sectors such as:
- Automotive
- Aerospace
- Electronics
- Medical
Its versatility and ability to handle diverse materials make it a valuable process in modern manufacturing.
Fourslide benefits
Fourslide stamping offers a slew of benefits over traditional metal stamping methods, including:
Cost-Effectiveness
Because of its ability to produce complex components in a single operation, fourslide stamping reduces production time and labor costs.
Optimal Precision
With the use of specialized equipment and advanced technology, fourslide stamping can achieve tight tolerances and intricate shapes with consistency and repeatability.
Reduced Waste
The fourslide design of the machine allows for efficient material utilization, reducing scrap waste and saving on material costs.
Faster Production
With its multi-slide design and advanced technology, fourslide stamping can produce large volumes of components at a rapid rate, increasing overall production efficiency.
Does fourslide stamping have any disadvantages?
While fourslide stamping offers numerous benefits, it also has a few potential drawbacks to consider. These include the initial cost of specialized equipment and tooling, as well as the need for skilled operators to ensure high precision and quality results. Additionally, this method requires a long setup time that may not work within certain time constraints.
Despite these limitations, fourslide stamping continues to gain popularity in various industries thanks to its versatility and efficiency in producing complex components.
Fourslide Stamping with Vogan Manufacturing
While fourslide stamping offers numerous benefits, it also has a few potential drawbacks to consider. These include the initial cost of specialized equipment and tooling, as well as the need for skilled operators to ensure high precision and quality results. Additionally, this method requires a long setup time that may not work within certain time constraints.
Despite these limitations, fourslide stamping continues to gain popularity in various industries thanks to its versatility and efficiency in producing complex components.